Recherche & Développement
Avec la volonté de conserver notre place de leader sur le marché de la mesure 3D sans contact et du contrôle qualité, nous nous devons d’être à la pointe de la technologie et d’adopter une démarche de recherche perpétuelle d’innovation. Ainsi notre Pôle R&D s’est fixé comme dessein de développer de nouvelles technologies et systèmes répondant aux besoins de nos clients. Nous réalisons des études de faisabilité et d’industrialisation. Ces dernières années nous avons mené et porté deux grands projets :
TOCATA: TECHNOLOGIE OPTIQUE COUPLÉE À L’ANALYSE TOPOLOGIQUE AUTOMATISÉE
Ce projet vise à développer une nouvelle technique CND de pièces après fabrication afin de palier au ressuage.
- - Technologie verte, alternative au ressuage,
- - Automatisation complète du procédé,
- - Traçabilité des défauts garantie,
- - Caractérisation du défaut via 3 méthodes de contrôle pour constituer une base de données de défauts certifiés par les industriels :
- Détection optique
- Détection par Courants de Foucault
- Détection par thermographie active
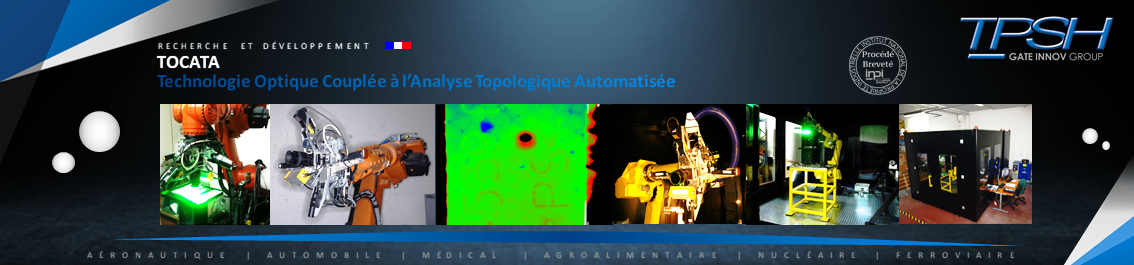
FALAFEL: Fabrication Additive par procédés LAser et Faisceau d’Electrons
- - Technologie de fabrication additive (DMD et SLM) de pièces grandes dimensions pour l’aéronautique,
- - Utilisation d’alliages certifiés aéronautiques,
- - Automatisation complète du cycle de fabrication,
- - Correction temps réel des dérives de fabrication,
- - Monitoring des machines DMD et SLM,
- - Traçabilité de fabrication,
- - Stockage sélectif des paramètres physiques et géométriques du bain de fusion,
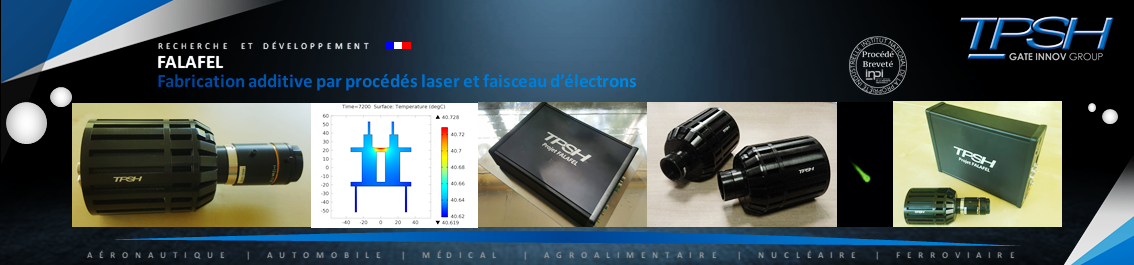
PAM-PROD: PROCÉDÉS ADDITIVE MANUFACTURING – PRODUCTIVITÉ (2019)
TPSH a la charge le contrôle de procédé temps réel MAG LASER et CLAD pour garantir la conformité des futures pièces fabriquées par la machine hybride. Le processus de contrôle se fera grâce à la TCAM128-65, caméra multi spectrale, SWIR infrarouge visible, développée à 100% par TPSH.
Dans le projet PAMPROD, TPSH est en charge du développement de la partie contrôle, suivi et régulation temps réel du procédé. Sur cette partie TPSH développe un réseau de caméra sensible dans l’infra-rouge permettant :
- - De suivre en temps réel les paramètres des bains de fusions,
- - D’analyser la conformité des paramètres de production,
- - D’envoyer des signaux de régulation ou de dérive en temps réel,
- - Et de réguler en temps réel les paramètres machine pour assurer la bonne conformité de la fabrication par le biais d’une « merging box » permettant la connexion temps réel a 1,5ms avec l’automate SIEMEN 840D de la machine de fabrication.
Le projet PAMPROD est la solution économique pour fabriquer des pièces de grandes dimensions, jusqu’à 5m en fabrication additive. Les machines sont équipées d’une solution hybride de fabrication additive, associant dépôt de poudre et dépôt de fil. Les technologies brevetées permettront d’assurer le suivi en temps réel des dépôts au niveau du bain de fusion grâce à notre système de visualisation alliant des caméras et une IHM. Une simulation thermomécanique, avant le lancement de la pièce en fabrication assurera la parfaite conformité de la pièce.

Retrouvez les actualités du projet PAMPROD sur LinkedIn
Et dans notre rubrique actualités:
Pour savoir plus sur le sujet, cliquez sur le lien.